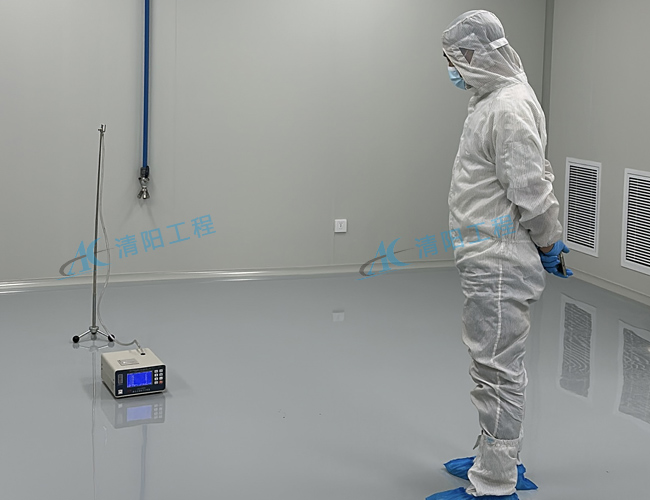
一、核心洁净度指标
1. 悬浮粒子浓度
- 精准定义:依据ISO 14644 - 1标准,十万级净化车间每立方米空气中,≥0.5μm粒子数被严格限制在≤3,520,000个,≥5μm粒子数≤29,300个。这一精确的量化标准,如同为车间的空气洁净程度划定了明确的界限。
- 对比优势:与普通室内环境相比,其粒子浓度仅为后者的1/100,展现出显著的洁净优势。然而,相较于芯片制造等百级车间,它又相对宽松约100倍。这种恰到好处的平衡,既满足了众多行业对洁净环境的基本需求,又有效控制了建设成本,使其成为众多企业的理想选择。
- 实现路径:通过初效、中效、高效三级过滤的有机结合,并搭配15 - 20次/h的合理换气次数,如同为车间构建了一道严密的空气净化防线,将空气中的悬浮粒子有效过滤,确保车间内空气的洁净度始终维持在标准范围内。
2. 微生物控制
- 沉降菌标准:沉降菌作为衡量车间微生物污染程度的重要指标,要求在Φ90mm培养皿暴露30分钟的情况下,≤10 CFU/皿。这一标准确保了车间内微生物在静态条件下的沉降量处于较低水平。
- 浮游菌标准:浮游菌的动态监测指标为≤500 CFU/m³,实时反映车间内空气中微生物的悬浮数量,保证车间微生物环境的稳定性。
- 应用案例:在制药行业,该标准为口服固体制剂、外用药品等非无菌制剂的生产提供了适宜的微生物环境,有力保障了药品的质量安全。
二、环境参数控制
1. 温湿度精准调控
- 温度范围:将温度严格控制在18 - 26℃,且波动范围控制在±2℃以内。这一温度区间既能满足电子元件对防潮的要求,又能确保药品的稳定性,为不同行业的生产工艺提供了适宜的温度条件。
- 湿度范围:湿度维持在45% - 65%,波动范围±10%。当湿度低于30%时,静电电压可达万伏级,极易对电子元件造成损害;而湿度高于70%时,霉菌繁殖加速,可能引发微生物污染问题。因此,精准的湿度控制对于防止静电产生和微生物滋生至关重要。
- 实现技术:采用恒温恒湿空调机组与蒸汽加湿/冷冻除湿组合系统,具备快速响应能力,响应速度≤15分钟。这一先进的系统能够根据车间内温湿度的实时变化,迅速做出调整,确保温湿度始终稳定在设定范围内。
2. 压差梯度管理
- 压差标准:相邻洁净区压差需≥5Pa,例如十万级区相对非洁净区应保持这一压差。压差的合理设置,如同在不同洁净区域之间构建了一道无形的屏障,有效防止污染物的扩散。
- 气流方向:气流遵循从高洁净度区向低洁净度区单向流动的原则,这种有序的气流组织方式,极大地避免了交叉污染的风险,保证了各区域的洁净度不受干扰。
- 监测手段:通过压差传感器实时反馈压差数据,并联动风阀自动调节,实现压差的动态精准控制,确保车间内的压差始终符合标准要求。
三、建筑与设备设计特点
1. 围护结构
- 材质选择:采用50mm厚手工岩棉夹芯彩钢板,其防火等级达到A级,为车间提供了可靠的防火安全保障。同时,表面涂层具备抗静电性能,表面电阻控制在10⁶ - 10⁹Ω,有效防止静电吸附灰尘,维持车间内的洁净环境。
- 密封处理:阴阳角采用R50铝合金圆弧过渡,不仅美观,更重要的是消除了卫生死角。接缝处采用硅胶密封后,进行氦气泄漏检测,确保泄漏率≤0.01%,最大限度地保证了围护结构的密封性,防止外界污染物侵入。
- 照明设计:选用LED洁净灯,确保照度≥300lx,无频闪。嵌入式安装方式有效避免了积尘问题,为车间提供了明亮、洁净的照明环境。
2. 通风系统
- 换气次数:设定换气次数为15 - 20次/h,相较于万级车间,换气次数降低了30% - 40%,同时节能约25%。在满足车间空气洁净度要求的前提下,实现了能源的高效利用。
- 气流组织:根据车间层高的不同,灵活采用顶送侧回(适用于层高≥3m车间)或顶送下侧回(层高受限时)的气流组织方式,确保工作区风速稳定在0.2 - 0.4m/s,使空气在车间内均匀分布,有效提升了空气净化效果。
- 设备选型:采用组合式空调机组搭配FFU风机过滤单元的配置方式。组合式空调机组负责整体的空气处理,FFU风机过滤单元则可根据实际需求模块化调节局部洁净度,为车间提供了灵活、高效的通风净化解决方案。
四、典型应用场景与效益
1. 制药行业
- 适用范围:广泛应用于中药提取车间、原料药精烘包工序、口服固体制剂(片剂/胶囊)生产等环节。
- 效益显著:与非洁净车间相比,产品微生物污染率大幅降低90%,生产环境投诉减少80%。这不仅有效提升了药品质量,还极大地提高了企业的生产效率和市场声誉。
2. 电子行业
- 适用范围:在PCB板组装、LED封装、精密仪器组装等领域发挥着重要作用。
- 效益突出:十万级车间使电子元器件焊接不良率从5%降至1.5%,每年可为企业节约超百万元的返工成本,显著提高了企业的经济效益。
3. 食品行业
- 适用范围:适用于乳制品灌装、烘焙食品冷却包装、保健品生产等环节。
- 效益明显:可延长产品保质期30%,例如糕点类产品保质期从7天增至10天,同时微生物超标风险下降75%,有效保障了食品的质量安全,提升了产品的市场竞争力。
五、建设与运维关键点
1. 前期规划
- 工艺匹配:根据生产工艺精确确定洁净区面积,例如药品生产需预留15% - 20%的缓冲空间。合理的面积规划能够确保生产流程的顺畅进行,同时满足不同生产环节对洁净环境的需求。
- 节能设计:采用变风量空调系统(VAV),在负荷降低时节能率可达40%。这一节能设计不仅符合可持续发展的理念,还能为企业降低长期的运营成本。
2. 施工管控
- 洁净施工:分阶段控制洁净度,按照从一般区到十万级再到万级的顺序逐步推进,施工时严格控制人员密度≤0.5人/m²。这种科学的施工方式能够有效避免施工过程中的交叉污染,确保车间最终达到预期的洁净度标准。
- 验证要点:高效过滤器PAO检漏合格率必须达到100%,风速均匀性≤±15%。严格的验证要点是保证车间洁净度和通风效果的关键,确保净化系统的稳定运行。
3. 运维优化
- 检测周期:制定科学合理的检测周期,悬浮粒子每月检测1次,微生物每季度检测1次,压差每日记录。定期检测能够及时发现车间环境参数的变化,为运维决策提供准确依据。
- 能效提升:通过余热回收技术,如空调排风热回收效率≥60%,进一步降低能耗,实现节能减排的目标,提高车间的运营效益。
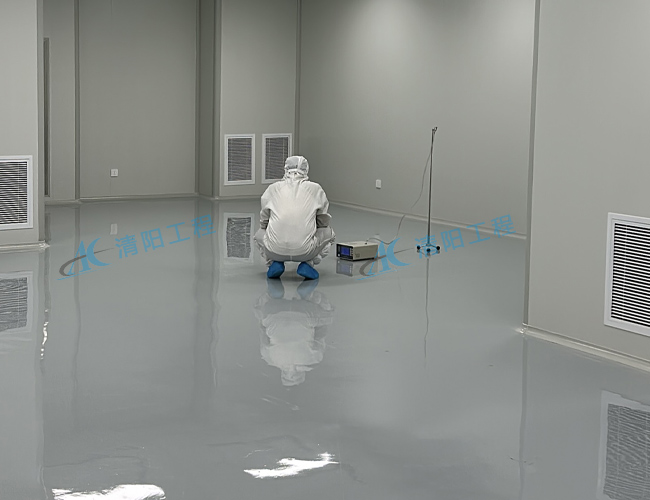
清阳工程可承接江浙沪皖等地区十万级、万级、百级、千级等各种洁净度等级的无尘车间的设计装修建设,我们有着17年的装修历史,各项资质齐全,承接过近500项净化工程。
欢迎微信咨询客服;或拨打全国服务热线:18015531058
- 下一篇: 洁净室层流罩的作用-清阳工程
- 上一篇:净化车间施工方案-清阳工程