在电子行业,净化车间的总体规划犹如一座大厦的蓝图,对于保障产品质量、提升生产效率以及确保安全环保至关重要。其规划需紧密围绕洁净度控制、生产流程优化及安全环保等核心方面展开。
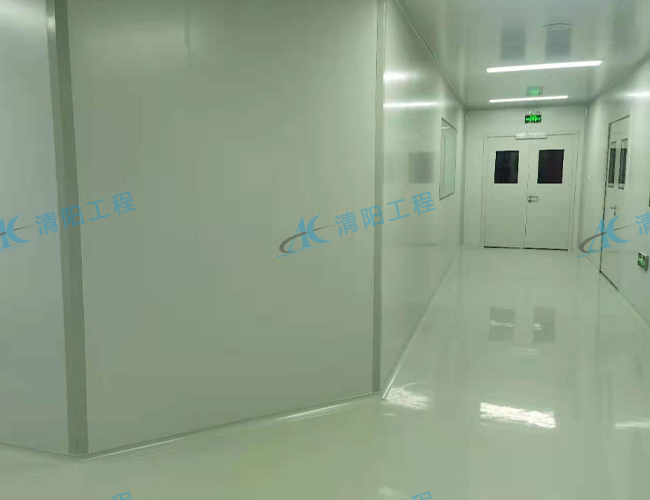
一、核心设计原则:塑造净化车间的架构灵魂
(一)洁净度分级控制
1. 分级的精准依据:依据电子生产工艺的独特要求,科学划分洁净等级区域。从 ISO 5 级到 ISO 8 级,不同的生产环节适配不同的洁净标准。例如,芯片封装这一核心工艺区,因其对微小颗粒极为敏感,必须达到 ISO 5 级的高洁净标准,以保障芯片的性能与质量;而组装测试区相对要求稍低,可设为 ISO 7 级。这种精准的分级,既满足了生产需求,又兼顾了成本效益。
2. 压差梯度的防护奥秘:通过巧妙设置梯度压差,即洁净度越高的区域气压越高,且相邻区域压差≥5Pa,为防止交叉污染构筑起一道坚实的防线。高气压区域的空气会自然流向低气压区域,从而有效阻止低洁净度区域的污染物侵入高洁净度区域,确保各生产区域的独立性与洁净度。
(二)功能分区与动线设计
1. 功能区的合理布局:精心划分功能区,核心生产区涵盖组装线与测试区,是生产的关键地带;辅助区用于设备维护与物料暂存,为生产提供有力支持;人员净化区包括更衣室与风淋室,确保进入洁净区的人员符合洁净要求;物流通道通过独立传递窗或货淋室,实现物料的安全传递。各功能区相互协作,共同保障生产流程的顺畅进行。
2. 人流动线的科学规划:人流动线采用严格的单向流动设计。人员进入车间需遵循换鞋→更衣(一更、二更)→风淋(≥15 秒)→洁净区的流程,杜绝折返造成的污染。这一设计理念旨在最大程度减少人员在车间内的交叉流动,降低污染风险,为洁净生产创造良好条件。
(三)灵活性与可扩展性
1. 模块化设计的前瞻性:采用大跨度柱网结构,如 15m、30m 跨度,为车间未来的工艺升级或规模扩展提供了极大的灵活性。模块化的设计使得车间内部空间易于重新布局,能够快速适应不断变化的生产需求,避免因结构限制而导致的大规模改造,节省时间与成本。
2. 预留空间的战略意义:在技术夹层、设备接口、配电系统等方面预留冗余,是为了适应未来设备增容的需求。随着电子技术的飞速发展,生产设备不断更新换代,预留充足的空间与接口,能够确保车间在不进行大规模重建的前提下,顺利实现设备升级与扩充,保持生产的连续性与先进性。
二、关键系统规划:构建净化车间的运行核心
(一)空气净化系统
1. 三级过滤的层层守护:空气净化系统采用初效(G4)→中效(F8)→高效(HEPA H13/H14)的三级过滤模式,如同三道紧密相连的防线。初效过滤器拦截大颗粒灰尘,中效过滤器进一步过滤较小颗粒,高效过滤器则对极微小的颗粒进行精准捕捉。末端送风采用 FFU 或高效送风口,确保送入车间的空气达到极高的洁净度。
2. 气流组织的优化策略:根据不同洁净区的要求,合理设计气流组织。高洁净区,如 ISO 5 级区域,采用垂直单向流,空气以均匀的速度垂直向下流动,能够迅速将污染物带出车间,保持空气的高度洁净;低洁净区则采用非单向流,如顶送侧回或顶送下回的方式,通过空气的混合与稀释,实现对污染物的有效控制。
3. 换气次数的精确调控:不同洁净等级对换气次数有严格要求。ISO 5 级区域≥300 次/小时,ISO 8 级区域≥15 次/小时。合适的换气次数是确保车间内颗粒物浓度达标的关键因素,通过频繁换气,不断更新空气,将污染物浓度控制在规定范围内。
(二)温湿度控制系统
1. 参数设定的科学依据:将温度设定在 22±2℃,湿度控制在 45% - 60%,这一范围主要是基于电子生产中对防静电的需求。适宜的温湿度环境能够有效减少静电的产生,避免静电对电子元件造成损害,保障产品质量。恒温恒湿空调机组则承担起精准控制温湿度的重任,确保车间内环境始终稳定在设定范围内。
2. 实时监测的智能保障:配置温湿度传感器,实时采集车间内的温湿度数据,并将其接入中央控制系统,如 SCADA。一旦数据出现异常,系统将自动报警,提醒工作人员及时采取措施进行调整,确保温湿度始终处于适宜的生产区间。
(三)防静电与安全设计
1. 静电防护的多重举措:在电子生产中,静电是一大隐患。因此,采取多种静电防护措施至关重要。设备、工作台、地板进行接地处理,使静电能够迅速导入大地;使用防静电涂料或材料,从源头减少静电的产生;配置离子风机,及时消除局部静电,确保生产环境的静电安全。
2. 防火安全的全面布局:设置自动喷水灭火系统、烟雾报警系统以及紧急疏散通道,为车间的消防安全提供全方位保障。关键设备更是自带火灾报警和灭火装置,一旦发生火灾,能够迅速响应,将损失降到最低,确保人员与设备的安全。
四、建筑结构与材料:打造净化车间的坚实躯壳
(一)围护结构
1. 墙体与吊顶的精心选材:墙体与吊顶选用金属夹芯板,如彩钢板、不锈钢板,或者抗静电 PVC 板。这些材料不仅具有良好的强度与防火性能,而且表面光滑,易于清洁。接缝处进行密封处理,吊顶做到平整无缝隙,有效防止灰尘与微生物的积聚,维持车间的洁净环境。
2. 地面的针对性选择:高洁净区选用环氧自流平地面,其具有优异的平整度与耐磨性,能够满足高精度生产的需求;一般区域采用 PVC 导静电地板,既能有效导除静电,又具备良好的经济性。地板接缝焊接密封,电阻值控制在 10⁴ - 10⁹Ω,确保静电防护性能达标。
3. 门窗的密封设计:洁净门采用不锈钢或铝合金材质,密闭无门槛,方便人员与物料通行的同时,保证良好的密封性。观察窗使用双层中空玻璃,边缘进行密封处理,既满足观察需求,又防止外界污染物进入车间。
(二)管道与布线
1. 隐蔽设计的洁净考量:风管、水管、电缆桥架采用暗装或隐藏于夹层的方式,最大程度减少在洁净区的暴露。这样的设计不仅美观,更重要的是避免了管道与线路表面积尘,降低对洁净区空气的污染风险。
2. 材料选择的质量把控:管道选用不锈钢材质,有效避免锈蚀污染;电气线路采用阻燃电缆,并穿管敷设,提高电气安全性,防止因电气故障引发火灾,保障车间的整体安全。
五、辅助系统与设备:完善净化车间的功能拼图
(一)照明系统
采用嵌入式 LED 洁净灯具,具备密封防尘的特性,确保灯具内部不会积尘,影响照明效果。照度方面,整体车间≥300lux,关键操作区≥500lux,且采用无影设计,为生产操作提供清晰、均匀的照明环境,提高工作效率与产品质量。
(二)环境监测系统
1. 实时监控的全面覆盖:安装在线粒子计数器、压差传感器、温湿度传感器,对车间内的洁净度、压差、温湿度等关键参数进行实时监控,并将数据接入中央控制系统。通过全面、实时的数据采集,工作人员能够随时掌握车间环境状况。
2. 报警功能的及时响应:一旦洁净度、温湿度、压差等参数出现异常,系统将自动报警。及时的报警机制能够确保工作人员迅速发现问题,并采取相应措施进行处理,避免因环境参数异常对生产造成不良影响。
六、施工与验收:确保净化车间的品质底线
(一)施工管理
1. 材料检验的严格把关:对装修材料和净化设备进行严格的质量检验,确保其符合设计要求和相关标准。从源头把控质量,避免不合格材料与设备进入施工现场,为车间的整体质量奠定基础。
2. 隐蔽工程的细致检查:在安装彩钢板墙面时,仔细检查拼接缝是否严密,防止出现漏风、积尘等问题;安装空气净化设备时,确认位置准确、连接牢固,保证设备的正常运行与净化效果。隐蔽工程的质量直接影响车间的长期使用性能,必须严格把控。
(二)验收标准
1. 洁净度检测的规范遵循:依据 ISO 14644 标准,对粒子浓度、压差、气流流型、泄漏测试等关键指标进行检测,确保各项指标均达标。洁净度是净化车间的核心指标,严格的检测是保障车间洁净性能的关键环节。
2. 功能测试的模拟验证:对温湿度控制系统、防静电系统、消防设施等进行模拟运行验证,确保各系统在实际运行中能够正常发挥功能。通过模拟真实的使用场景,全面检验各系统的可靠性与稳定性。
七、日常运维与优化:持续提升净化车间的运行效能
(一)维护计划
1. 过滤器的定期更换:定期更换初效、中效、高效过滤器,是确保空气净化效率的关键措施。随着使用时间的增加,过滤器会逐渐积累灰尘,过滤效果下降。定期更换过滤器,能够保证空气净化系统始终处于高效运行状态,维持车间的洁净度。
2. 清洁消毒的规范执行:对地面、墙面、设备进行定期清洁和消毒,防止积尘和微生物滋生。规范的清洁消毒工作不仅有助于保持车间的洁净环境,还能延长设备的使用寿命,提高生产效率。
(二)人员培训
1. 操作规范的强化培训:对员工进行无尘车间操作规范、静电防护、洁净度意识等方面的培训,使员工深刻理解并严格遵守相关规定。规范的操作是保障车间洁净度与生产安全的基础,通过培训提高员工的操作技能与意识至关重要。
2. 应急演练的定期开展:定期组织消防、疏散等应急演练,提升员工的安全意识与应急处理能力。在面对突发紧急情况时,员工能够迅速、有序地采取应对措施,最大程度保障人员生命安全与减少财产损失。
(三)持续改进
1. 数据驱动的优化策略:通过环境监测系统收集的数据,深入分析洁净度波动的原因,进而优化净化系统的运行参数。数据是车间运行状况的直观反映,基于数据的分析能够发现潜在问题,并针对性地进行优化,不断提升车间的洁净度与稳定性。
2. 流程优化的效率提升:根据生产需求,适时调整功能区布局,减少物料搬运距离,提高生产效率。随着生产工艺与产品的变化,及时优化车间流程,能够使车间的运行更加顺畅,适应市场的发展需求。

清阳工程可承接江浙沪皖等地区十万级、万级、百级、千级等各种洁净度等级的无尘车间的设计装修建设,我们有着17年的装修历史,各项资质齐全,承接过近500项净化工程。
欢迎微信咨询客服;或拨打全国服务热线:18015531058
- 下一篇: 最后一页
- 上一篇:净化车间装修多少钱一平米?-清阳工程